Group News: 2015
FORTIES: The Field that keeps giving: 2010 - 2015
In 2009, Offshore Group Newcastle (OGN) had completed a concept study for a simple wellhead tower at Delta - just as Apache was completing one for Alpha. By the end of 2009, the resolution was to integrate both studies into a functional specification for a new bridge-linked platform, FASP, which would be positioned next to Alpha. In 2010, a £400 million ($648 million) contract for the construction of the FASP was initiated and work began. Float out of the FASP carbon steel jacket was in September 2012 with final commissioning in August 2013.
On joining the ring main, FASP has provided an additional two turbine generators of power. It has a production capacity of 25,000 barrels per day and provides 18 new slots for drilling additional development wells to target the pockets of oil that were inaccessible from Forties Alpha. Together with Apache’s various other upgrades and improvements, it has extended the life expectancy of the Forties field by 20 years.
2012 also saw first oil from the Bacchus field. Bacchus lies around 6.5km North East of Forties Alpha, in Block 22/6s North and was discovered in July 2005 with well 22/6a-14. Oil from Bacchus travels to the Forties Alpha platform via a 6.7km subsea bundled pipeline.
By 2013, Apache had invested £2.8 Billion ($4.3 billion) in the Forties field since its acquisition. It had produced 190 million barrels of oil equivalent, and its average daily production stood at 60,000 barrels per day.
Following the success of Bacchus, the Aviat subsea field development will be the second subsea tie-back to Forties and aims to provide fuel gas to the field. Providing up to 19 million standard cubic feet per day of fuel gas, this valuable source of fuel will help sustain Forties production for 15 years or more, in line with latest production forecasts and development of future targets.
Project Talk: Monitor Systems supplies the Forties Delta Platform with (Total Gas & H2S Gas Detection System in Mud). Read the news article, click-here.
Monitoring Cold Stacked Rigs
History shows us that the decline in oil prices over a sustained period of time is the primary contributing factor for oil drilling contractors to set about ‘cold stacking’ rigs. The secondary factor is the cyclical downturn in demand for a given rig design / type.
Many oil contractors look at ‘warm stacking’ prior to ‘cold stacking’ rigs, as they hope that the market will turn around quickly, however in a sustained period of reduced oil prices, cold stacking is sometimes the only economical and viable solution until there is a significant recovery.
Cold stacking inevitably means that workers are let go and the rig is completely shut down. Cold stacking a rig involves reducing the crew to either zero or just a few key individuals and storing the rig in a harbour, shipyard or designated area offshore.
Typically, steps are taken to protect the cold stacked rig including the installation of monitoring systems that communicate rig status and critical systems information to locations onshore.
Monitor Systems provides a comprehensive marking and monitoring system that can include GPS Position Monitoring, Intruder Monitoring, Fire and Bilge Alarm Monitoring, Anchor Winch Tension Monitoring, (AIS) Automatic Identification System, all powered by a solar power supply.
Typical Scope of Work: The marking and monitoring of cold stacked rigs involves a comprehensive ‘scope of work’ that includes Project Management, Conceptual Design, QA & HS&E Management (ISO 9001 Compliant), Engineering and Manufacture, System Testing, Software Interrogation and System Documentation.
Brief Overview / Marking and Monitoring System: The cold stacked rig is ‘marked’ by the use of navigational obstruction lights and the rigs position is monitored and relayed to a monitoring station in the Port Authority’s Office. The stacked rig is also fitted with an Automatic Identification System (AIS) transmitter which transmits its position every three minutes. Our marking and monitoring system can monitor the bilge alarms, anchor winch tensions, fire alarms and intruder monitoring and any other required signals, with signals marshalled into a local process enclosure and terminated onto a wireless I/O module to be transmitted over UHF. The hardware fitted to the unmanned rig is powered by solar/wind power and is fully operational 365 days per year.
For full system details, please click-here
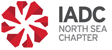







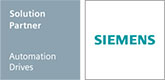

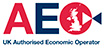

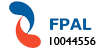