Group News: 2017
MGS (Mud Gas Separator) Vent Valve Control System
Monitor Systems were approached by a new global client to design, manufacture, test, DNV approve and supply a MGS (Mud Gas Separator) Vent Valve Control System for an offshore application.
The MGS (Mud Gas Separator) Vent Valve Control System controls the opening and closing of the valves on the vent lines for the mud gas separator (MGS), degasser 1 and degasser 2. Each of these have a vent line running to both the port and starboard sides of the rig, with a valve situated on each line to allow the venting of gas to be directed to the port or starboard sides.
SCOPE: The MGS (Mud Gas Separator) Vent Valve Control System comprises a PLC control panel, a field control panel, a pneumatic panel and six vent line valves. The system was project managed, designed, manufactured and tested in-house, and included system approval submission to DNV.
PLC Control Panel: This panel houses all of the processing hardware and features door facia mounted controls and indicators. The panel will be mounted in the WOCC and is suitable for safe area use only.
Field Control Panel: this panel has door facia mounted controls and indicators terminated into an internally mounted Exe IECEx / ATEX junction box which is interconnected to the PLC control panel via two field cables. The field control panel will be mounted on the well test mezzanine deck and is compliant to zone 1 operation.
Pneumatic Panel: this panel contains the dual coil solenoid valves for actuation of the pneumatic vent valves. The panel will be installed in the Bosun Store and is suitable for safe area use only. The panel features five 10mm OD stainless steel bulkheads for connecting an air supply, including four valve control lines.
Valves: Two different valve types have been supplied, both of which are pneumatic ‘spring return to closed’ valves. Two 8” valves were used for the MGS Mud Gas Separator port and starboard lines, and four 4” valves were used for the degasser 1, 2 port and starboard lines. All valves were connected to the system through an Exe IECEx / ATEX rated junction box which was originally intended to be installed local to the valves on the well test mezzanine deck, and is therefore suitable for use in zone 1. This was finally installed in the Bosun Store below the mezzanine deck.
Brian Sinclair (MD) commented ... "designing bespoke engineering solutions for hazardous area applications is one of our many in-house strengths, and draws on our many years of industry expertise and engineering knowledge. Monitor Systems were delighted to be awarded this project, it gave us the opportunity to demonstrate our capability, and our ability to deliver projects on time and within budget."
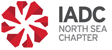







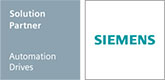

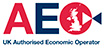

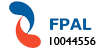